Navigate Your CNC Career: Training, Certification, and Opportunities in the U.S.
1. introduction
CNC (Computer Numerical Control) machinists are indispensable in modern manufacturing. They operate and program CNC machines to produce highly precise parts for critical industries such as aerospace, automotive, and medical devices. With the continuous growth of automation, the demand for skilled CNC machinists is on the rise. According to the U.S. Bureau of Labor Statistics (BLS), employment for CNC machinists is projected to grow by 6% from 2020 to 2030, outpacing the average growth rate for all occupations. This increasing demand is driven by the need for precision and efficiency in manufacturing processes.
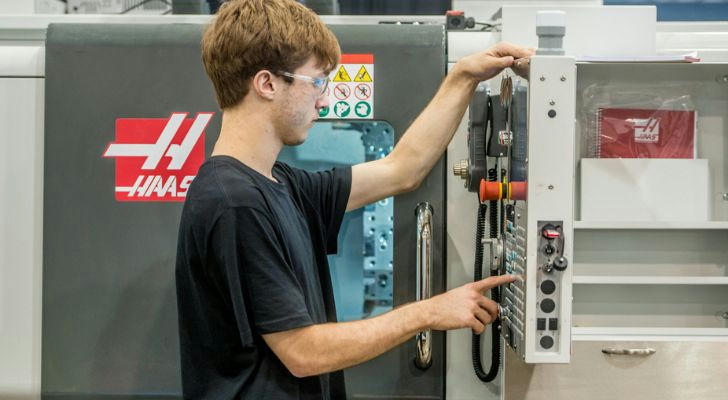
2. Responsibilities and Skills of CNC Machinists
Job Responsibilities
CNC machinists are responsible for operating and programming CNC machines to produce parts that meet technical specifications. Their primary tasks include:
Operating CNC Machines: Running lathes, mills, and grinders to manufacture components.
Programming CNC Machines: Writing and editing CNC programs using specialized languages such as G-code.
Reading Mechanical Drawings: Interpreting technical blueprints to ensure parts adhere to design specifications.
Machine Maintenance: Ensuring machines remain accurate and efficient through regular maintenance.
Quality Control: Measuring parts with tools like calipers and micrometers to verify they meet required standards.
Essential Skills
To excel in this field, CNC machinists need to possess several key skills:
CNC Programming: The ability to write, adjust, and optimize CNC programs.
Blueprint Reading: Understanding technical drawings to create accurate parts.
Precision Measurement: Proficiency in using measurement tools such as micrometers and calipers.
Troubleshooting: Quickly diagnosing and resolving issues during production.
Safety Knowledge: Strict adherence to safety protocols when working with heavy machinery.
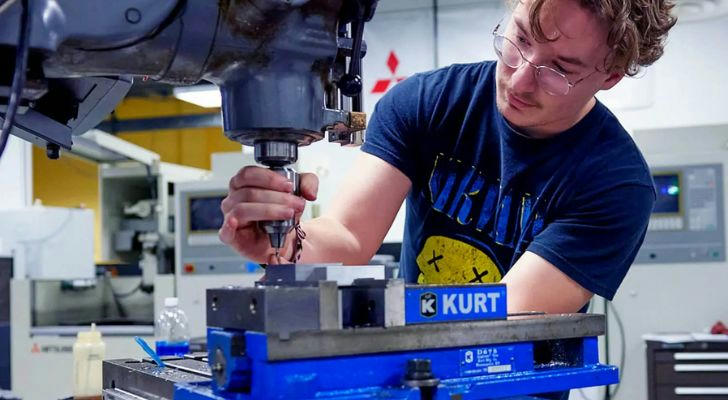
3. Types of CNC Machinist Training Programs
There are various training programs available for aspiring CNC machinists:
Apprenticeship Training: Combining hands-on experience with classroom learning, apprenticeships typically last 3-4 years. Apprentices earn wages while learning from experienced machinists, gaining valuable practical skills.
Technical College Programs: Technical colleges offer two-year programs in CNC machining, programming, and mechanical drawing. Graduates earn certificates or associate degrees, which prepare them for diverse career opportunities in the industry.
Online Courses and Certifications: Online programs provide flexibility, allowing students to learn at their own pace. However, practical training is still necessary. Certifications from reputable organizations like NIMS (National Institute for Metalworking Skills) can significantly enhance job prospects.
4. CNC Training Program Content
Training programs cover essential topics to equip students with the necessary skills:
CNC Machine Operation: Students learn to operate lathes, mills, and grinders effectively.
CNC Programming: Training focuses on writing and editing machine programs using specialized software and languages.
Mechanical Drawing Interpretation: Students gain the ability to understand and interpret technical blueprints.
Quality Control: Emphasis is placed on using measurement tools to ensure precision and accuracy.
Safety: Learning and adhering to safety protocols for machine operation is crucial to prevent accidents.
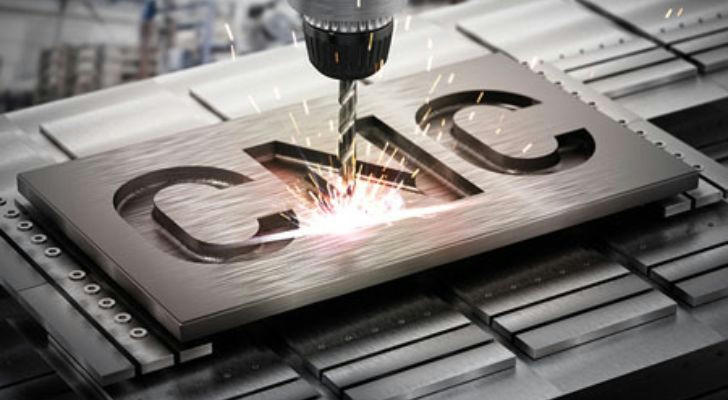
5. Certification and Qualifications
While certification is not always mandatory, it can significantly enhance job prospects and earning potential. Certification programs, such as those offered by NIMS, validate skills in areas like programming and machine operation. Common certifications include:
CNC Operator: Demonstrates proficiency in machine operation.
CNC Programmer: Indicates expertise in writing CNC programs.
CNC Setup and Operation: Shows efficiency in machine setup and operation.
Certified machinists tend to earn higher wages. According to BLS data, certified CNC machinists earn a median salary of $57,000, compared to lower earnings for those without certification.
6. Career Development and Salary
CNC machinists have a wide range of career opportunities, with the potential to advance into higher-paying roles:
Entry-Level Machinists: These positions typically involve working under more experienced machinists and offer lower pay.
CNC Programmers: With additional experience, machinists can transition into programming roles, which offer higher salaries.
Engineering or Supervisory Roles: Experienced machinists may advance to engineering or management positions, overseeing projects and teams.
Salary expectations vary by role. According to BLS data, CNC operators earn a median salary of $44,420, while CNC programmers make a median of $57,000. As machinists gain experience, their salaries can increase significantly.
7. Challenges and Opportunities
CNC machinists face several challenges, including:
High Skill Demands: The role requires a diverse skill set, encompassing machine operation, programming, and troubleshooting.
Workplace Risks: Handling heavy machinery can be hazardous, making adherence to safety protocols essential.
Despite these challenges, CNC machinists are in high demand, offering strong job security and competitive salaries. The continuous evolution of automation and precision technologies creates ongoing opportunities for skilled professionals in this field.
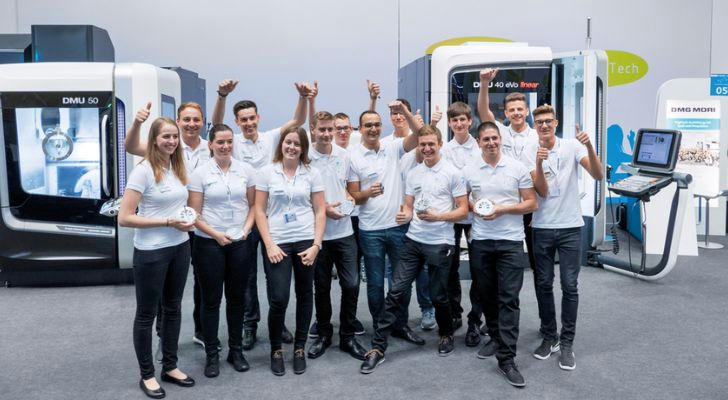
8. Conclusion
CNC machinists are vital to manufacturing industries, playing a crucial role in the production of high-precision components. As automation and precision technologies advance, the demand for skilled machinists is expected to grow. Training programs—through apprenticeships, technical colleges, or online courses—provide various pathways into this rewarding field. With proper training and certification, CNC machinists can enjoy excellent career opportunities, competitive salaries, and the satisfaction of contributing to modern manufacturing processes. As industries increasingly demand precision, CNC machinists will remain an essential part of the manufacturing landscape.